The InMotion team has been looking closely at investment opportunities tied to reducing our industry’s carbon footprint and promoting ethical business practices. The current lockdown notwithstanding, these topics remain a top priority for Jaguar Land Rover and the wider industry. Our research concludes that making a strong environmental impact by designing sustainable products and business processes underpinning them can benefit the bottom line. This article highlights four key areas of innovation, each with the potential to deliver new revenue streams and a lower cost base, helping automotive companies reach their sustainability targets.
Cars contain on average 1.4 tonnes of material. Traditionally only a proportion of this material, mainly metal, was recovered and recycled at the end of a vehicle’s life cycle. The circular economy moves away from the current linear ‘take-make-dispose’ model towards a ‘reduce-reuse-recycle’ model. It is an economic system which is primarily aimed at reducing carbon emissions, waste and resource extraction. The estimated economic benefit of having such an industrial system that is ‘restorative by intention and design’ is more than $1 trillion a year in material savings alone.
Within the automotive sector we have begun to see circular systems employ enhanced reuse, sharing, repair, remanufacturing and recycling practices, involving entire value chains. By investing more in design and improving end-of-life management, the industry can capture economic value while reducing its environmental impact.
Raw material management, sustainable materials, waste as a resource and product life extension represent growing markets with accelerating demand where high investment in research and development is taking place. Investing in these four key areas allows OEMs to stay ahead of regulators, and in touch with consumer sentiment.
- Raw Material Management: Comprises the energy efficient and ethical extraction of raw materials. Supply chain tracking technology can certify the material’s exact origin and ensure it is ethically sourced. It also creates greater transparency across the supply chain, allowing OEMs to set the bar for working practices they expect their suppliers to follow.
- Sustainable Materials: Comprises the creation of materials that are sustainable and have a low environmental impact throughout their life cycle. Novel technologies are producing new high-quality materials for vehicle interiors that enjoy increasing consumer uptake.
- Waste as a Resource: Defined as the process of recovering valuable materials from waste products in a sustainable way to create new materials. Breaking down waste plastics to their core chemical components allows recycling of materials with no downgrading of quality compared with using virgin material.
- Product Life Extension: Extending the working lifecycle of a vehicle through machine learning and effective management systems. The use of data-driven analytics has enormous potential to prolong the useful life of vehicles and their core components. Predictive maintenance in particular has ability to deliver significant cost savings.
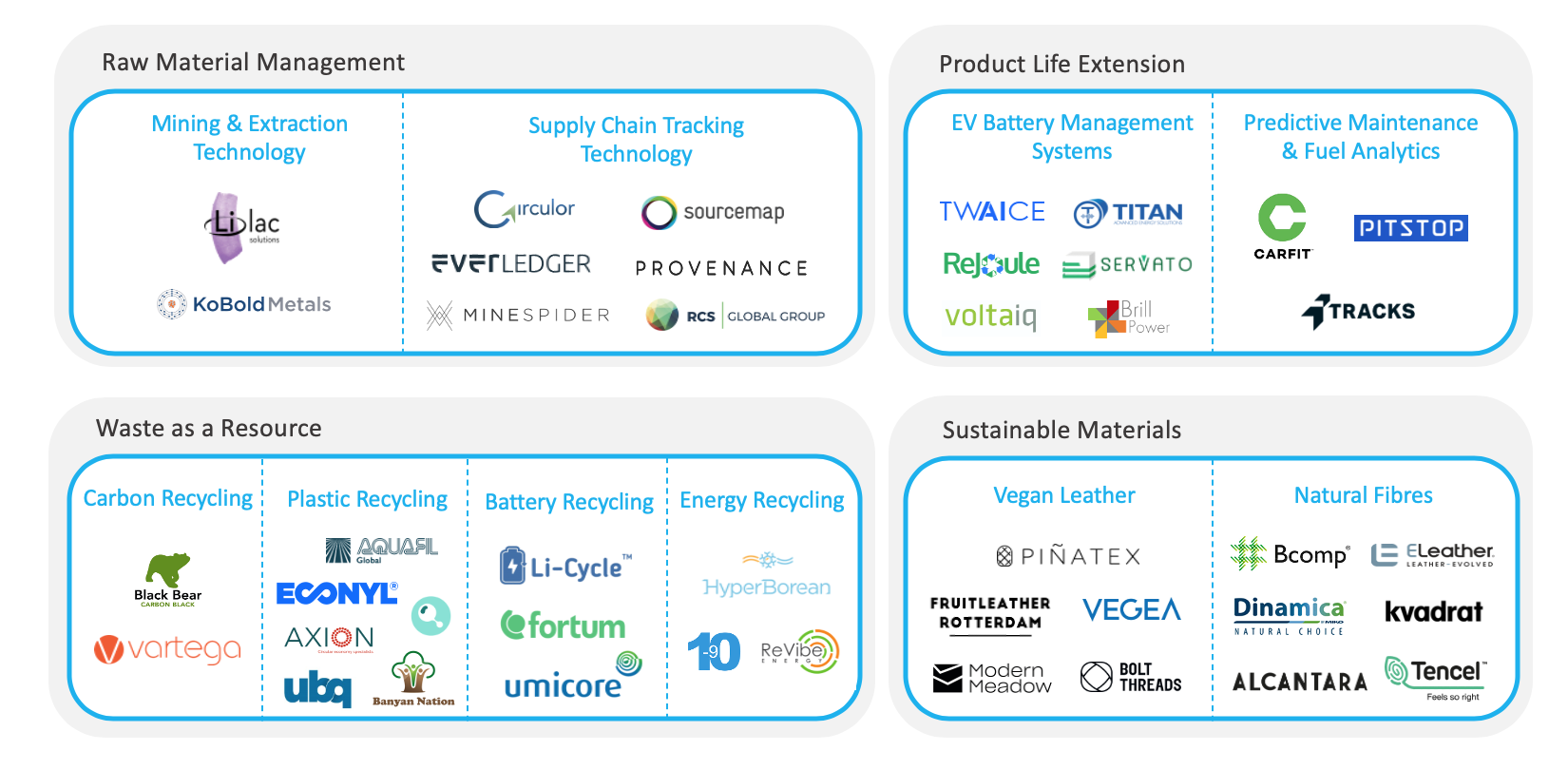
Raw Material Management
The growth of the electric vehicle market, regulatory interventions, supply shortages and consumer demands have placed a great amount of pressure on the battery value chain. As automotive manufacturers push to increase the production of EVs, an appropriate emphasis must be placed on ensuring a sustainable supply chain with ethical working practices.
The lithium-ion battery is currently without a commercial alternative as a power source for electric vehicles. The Nickel-Manganese-Cobalt (NMC) combination for the electrode material is the most common due to its long-lasting charge. However, both the supply of these metals and the ability to ensure that they are ethically sourced presents a great hurdle for automotive companies.
Circulor, a UK-based start-up, has developed an innovative digital platform to track such raw materials throughout the supply chains of large companies providing a digital ledger for both miners and consumer-facing companies using battery materials. The solution is actively used by OEMs to ensure they are meeting their commitment towards more ethical sourcing practices, and we expect such solutions to be widely adopted.
Sustainable Materials
The case for a sustainable vehicle interior is a compelling one. There is a pressing need to rethink the ‘take-make-dispose’ model. OEMs face increasing pressure to declare the provenance of materials such as leather, and to improve production processes. Localised sourcing is one solution. Bridge of Weir Leather Company in Scotland is often recognised as one of the most environmentally efficient leather manufacturers in the world and a key supplier of sustainable leather to the British automotive industry.
Low tolerances for imperfect markings in the automotive industry have traditionally resulted in high levels of waste. This creates a real incentive to make the switch to sustainable rollstock material where production can be controlled – provided quality is not compromised and consumer demand sustains such choices.
This opportunity has resulted in exciting innovations from start-ups developing vegan leather alternatives to both animal leather and inexpensive synthetic leather fabrics. Examples include Piñatex by Ananas Anam (a leather substitute made from pineapple leaf waste), Mylo by Bolt Threads (a mushroom-based leather alternative), and Zoa by Modern Meadows (leather alternative created from biologically produced collagen protein). These companies’ materials have become highly sought after by leading fashion brands and automotive OEMs. Piñatex has already caught the attention of H&M, Chanel, and Skoda.
The stringent specifications when it comes to material testing in automobiles mean that the application of sustainable materials is at an earlier stage of development than other industries. This represents an area of high growth and a chance to be an early stage adopter. Jaguar Land Rover has introduced sustainable material offerings in the interior upholstery for a number of their new vehicles including the Range Rover Velar, Range Rover Evoke and the Jaguar I-PACE. The fabric is made using recycled plastic bottles through a collaboration with textile firm Kvadrat. This is part of Jaguar Land Rover’s materiality strategy, which is not focused solely on non-leather alternative but instead orientated to ensure that processes as a whole are both sustainable and responsible.
Waste as a Resource
Waste as a resource is a business model that promotes circularity and is vital to the automotive industry. The approach ensures that raw materials such as aluminium, textiles, and plastics are recycled and kept in use as much as possible in the local automotive industry.
Plastic recycling is becoming ever more important in the age of EVs. The light weighting phenomenon, whereby car manufacturers are increasingly using more plastics in vehicles to offset the weight of the batteries means that the car is gradually becoming less circular in nature. Manufacturers are increasingly looking for more natural and environmentally friendly materials to be incorporated in their vehicles. The use of recycled plastics will be key in adhering to both regulatory and consumer demands. Advances in material sorting technology are key to enabling this reuse of waste. The longer-term goal is to lower the cost of recycled material over that of virgin materials, while not compromising on quality.
Jaguar Land Rover has been particular active in reducing waste from its manufacturing activities, achieving its zero-waste-to-landfill status for UK operations two years ahead of its 2020 deadline. The company launched its REALITY (recycled aluminium through innovative technology) project in 2017, a mission which aims to enable the closed-loop recycling of aluminium from end-of-life vehicles and reform it into a new high-grade aluminium to create new vehicles. ChemCycling is another exciting project in conjunction with the German chemical firm BASF that upcycles domestic waste plastic, otherwise destined for landfill or incinerators, into a new high-quality material that could feature on future vehicles.
It is not just OEMs paving the way, but a growing segment of startup innovators. One such company is Black Bear, a Dutch company that has reinvented tyre recycling. More than 3.6 million tonnes of tyres become waste each year in the EU alone. By upcycling end-of-life-tyres into high-quality carbon black, Black Bear is able to use these tyre waste streams to create a sustainable supply of raw materials in a constrained market.
Product Life Extension
Predictive maintenance is still very much in its infancy in the automotive industry, not yet reaching the levels of maturity as in other sectors such as aeronautics. Maintenance still follows a traditional method whereby a service is recommended to be undertaken every 30,000km or two years on average. This presents a great opportunity for automotive OEMs and fleet managers to harness the technology needed to extend the lifetime of their vehicles and generate a new revenue stream in the process. The recent rise of connected cars gives OEMs the opportunity to capitalise on the inflow of data they are collecting and subsequently offer remote diagnostic services. Revenues from new mobility services are expected to soar by 2030, with profits predicted to overtake those from vehicle sales.
Predictive maintenance combines both artificial intelligence (AI) and the Internet of Things (IoT) to help manufacturers compare real-time data from sensors on connected equipment to its historical performance data. For connected cars, this real-time information can help automotive OEMs and fleet managers accurately measure the condition of their vehicles and predict the need for replacement parts.
Batteries are a core component of EVs. EV manufacturers who choose to adopt battery management systems such as TWAICE can expect a reduction of overall operating costs. The ability to accurately project the precise conditions of batteries greatly optimises battery development and use. A longer battery life increases the sustainability of electrical mobility.
An estimated 1.2 billion excess tonnes of CO2 emissions are produced each year in North America as a result of poor vehicle maintenance. Car Fit and Pitstop are two standout companies deploying technology that analyses car data through machine learning. The sensor technology and algorithms used are able to perform predictive maintenance in cars to identify patterns of degradation and faults before they become a problem, making vehicles both greener and safer as a result.
Conclusion
The automotive industry has reacted to mounting pressures from policy makers and consumers to embrace the circular economy. Soaring prices of raw materials and advances in technology create opportunities to capture economic value from the circular economy. Leading companies recognise this opportunity. They drive new revenue streams and harness new circular technologies to lower their cost base while responding to consumer demands. Many of the leading car manufacturers have ambitious sustainability goals, which include lowering carbon emissions throughout production processes and ensuring that a high percentage of the material going into vehicles is recyclable.
The four themes highlighted represent areas and technologies are still at a relatively early stage of development and start to have a transformative impact on industry working practises. Reimagining processes around manufacturing and design, including a distinction between a product’s consumable and durable components, is vital. To stay in touch with consumer sentiment and ahead of the regulator, OEMs need to continuously innovate and adapt existing products and services to have a real and lasting impact in a circular economy.
Authored by Louis Fearn